The manufacturing industry is filled with opportunity, innovation, and efficiency. But operating a manufacturing plant requires careful planning and execution from all levels to ensure maximum proficiency in operations. Although having an efficient operation can be achieved with the right approach, there are many businesses that struggle to understand how best to run their plants.
In this post, we’ll delve into what it takes to achieve operational excellence in the manufacturing sector; exploring topics such as process optimization, system integration, and more — adding valuable insight into running an effective production line.
Lean manufacturing
In today’s hyper-competitive global marketplace, manufacturing plants need to operate at maximum efficiency to stay ahead of the competition. Lean manufacturing principles provide a proven framework to achieve this goal, by eliminating waste and optimizing processes.
By implementing lean practices throughout the plant from the front office to the factory floor, companies can streamline operations, reduce costs, and drive productivity. From reducing setup times to improving supply chain management, lean manufacturing offers a comprehensive approach to boosting efficiency and competitiveness.
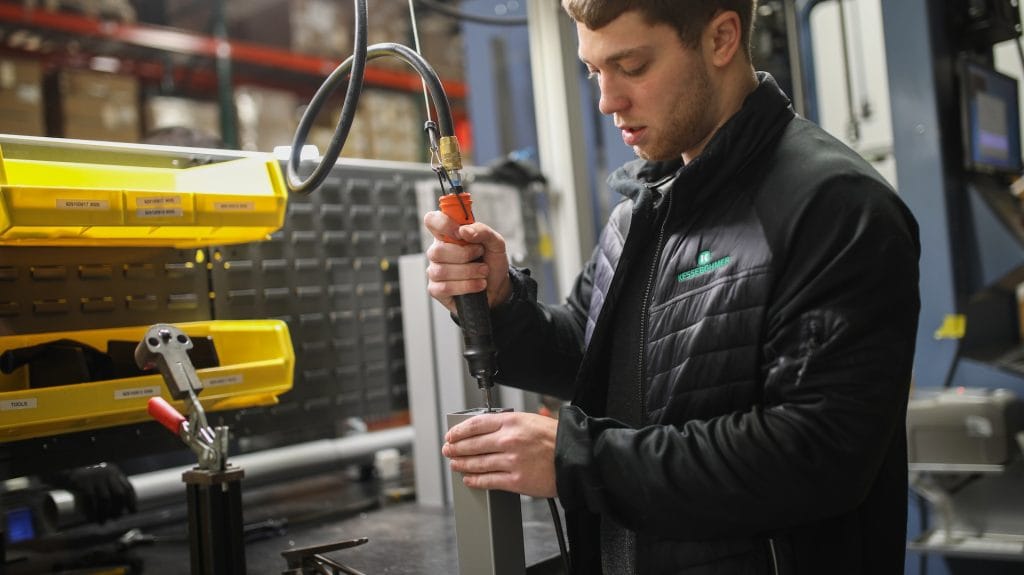
Automation and robotics
The manufacturing industry is constantly seeking ways to improve operational efficiency and output. One solution that has been gaining popularity is the integration of advanced automation and robotics systems.
By incorporating industrial computers and robotic technology into manufacturing operations, businesses can significantly improve productivity, accuracy, and speed. The benefits of automation are undeniable – it reduces human error, allows for more precise and consistent quality control, and can increase output levels while decreasing the amount of time it takes to complete tasks.
The use of industrial computers and robotics is changing the manufacturing industry, and businesses that adopt these technologies are positioning themselves for greater success.
Supply chain management
In the highly competitive world of manufacturing, efficient operations are key to staying ahead of the game. To achieve this, streamlining the supply chain is essential. One way to do this is by optimizing inventory management. Ensuring that you have the right inventory available at the right time can reduce waste and minimize storage costs.
Implementing just-in-time practices is another way to improve supply chain efficiency. This involves getting raw materials and other inputs only when they are needed and in the quantities required. Finally, fostering strong relationships with suppliers can help to ensure that your supply chain operates smoothly.
By working collaboratively and communicating effectively, both parties can benefit, and the overall manufacturing process can become more streamlined.
Continuous improvement
Efficient operations are at the heart of any successful manufacturing plant. That’s why cultivating a culture of continuous improvement is critical to stay ahead of the competition. By encouraging employee engagement and providing regular feedback loops, manufacturing plants can more easily identify areas for improvement and drive operational enhancements.
Creating such a culture takes time and effort, but the benefits are clear. A team that is constantly seeking ways to improve processes and procedures leads to increased productivity, improved product quality, and reduced costs. It’s a win-win situation that all manufacturing plants should strive for.
Quality control systems
Manufacturing plants are often faced with the challenge of producing products with consistent quality levels. Implementing quality control systems can help to mitigate this issue by ensuring strict adherence to manufacturing processes. Effective quality control methodologies involve using tools such as Six Sigma and statistical process control to minimize the variability of product outputs.
The Six Sigma methodology is a data-driven approach that seeks to eliminate defects in manufacturing processes through a consistent and repeatable approach. Statistical process control, on the other hand, uses statistical analysis to monitor and improve manufacturing processes by identifying potential issues before they become major problems.
By adopting these methodologies to implement robust quality control measures, manufacturing plants can streamline their operations and improve their overall efficiency, ultimately leading to a better end product for their customers.
Maintenance and asset management
Another key aspect of achieving efficiency is maintenance and asset management. Utilizing proactive maintenance strategies, predictive maintenance technologies, and effective asset management practices can go a long way in minimizing downtime and maximizing equipment utilization.
Properly identified and planned maintenance can prevent equipment breakdowns and help identify potential issues before they occur. This allows for more efficient use of resources, as well as better decision-making when it comes to equipment replacement or upgrades.
Employee training and development
One critical component of efficient operations is investing in employee training and development. By providing comprehensive training programs and skill development initiatives, manufacturing plant employees can acquire the knowledge and tools they need to excel in their roles.
Additionally, fostering cross-functional teamwork enables employees to collaborate and tackle challenges together, ultimately enhancing overall operational efficiency. When manufacturing plants prioritize employee training and development, they invest not only in their workforce but also in the long-term success of their business.